Rotational Molding
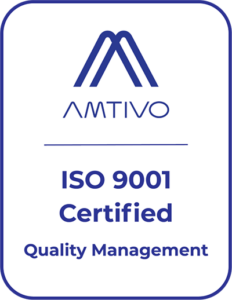
Why Forté Products for Custom Rotational Molding?
Primarily, our customers appreciate our flat organizational hierarchy that promotes direct communication and unparalleled responsiveness. In addition, we offer more than a dozen, various-sized machines in two Midwest plants. Our expertise comes from manufacturing nearly 300,000 custom, rotationally molded plastic parts each year. We serve hundreds of customers, across dozens of industries. We have particular expertise with large, commercial parts: fertilizer and water tanks; waste receptacles; foam-filled boats as examples. If you can imagine it, we can mold it for you.
Forté Products Rotational Molding Highlights
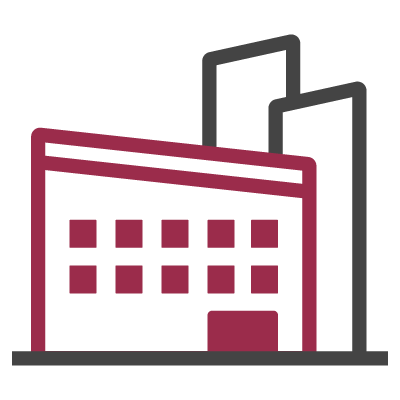
2 Separate Facilities in the Midwest
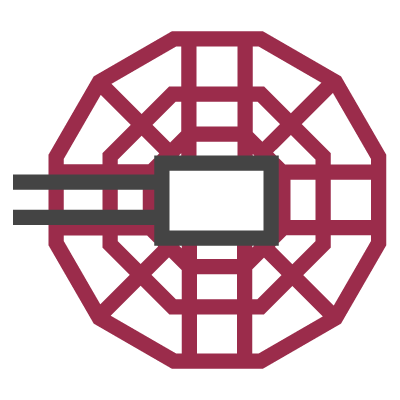
A dozen machines manufacturing parts up to 288” x 120”
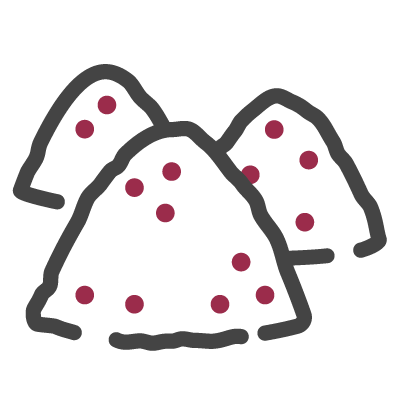
Expertise with LLDPE, HDPE, XLPE and Nylon
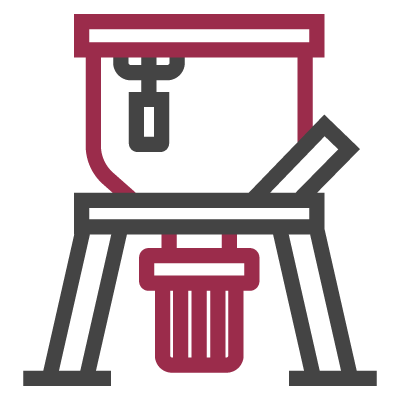
In-house resin pulverizing and color blending
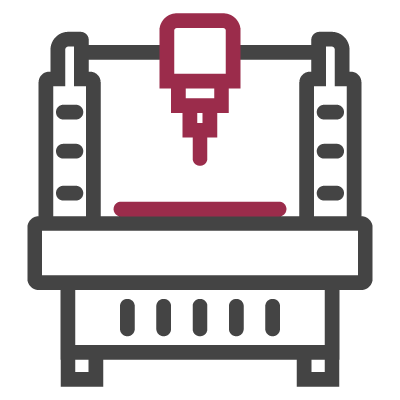
5-Axis CNC trimming/finishing
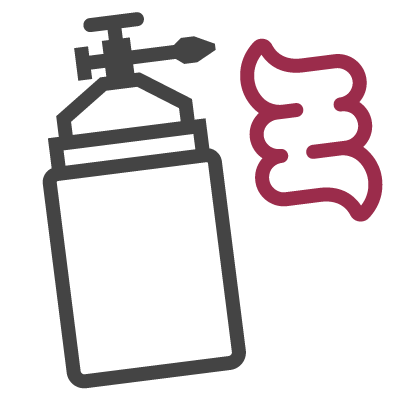
Foam Filling expertise
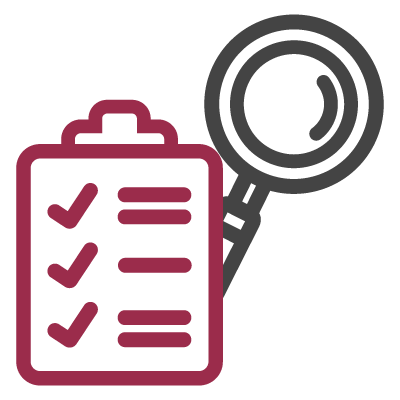
“Moldability” Engineering Assessment
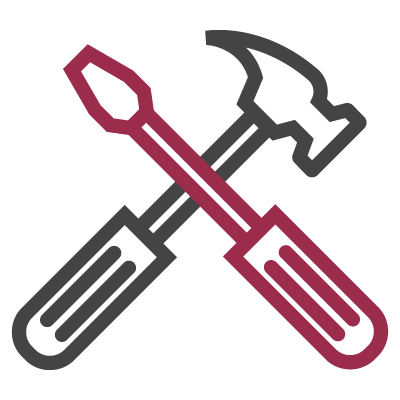
In-house tool maintenance
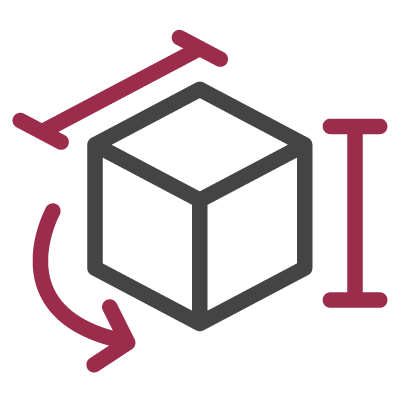
Finishing fixture design and fabrication